
While less common than kinematic viscosity, absolute viscosity and the Brookfield viscometer are used in formulating engine oils. This method is commonly referred to as the Brookfield method and is described in ASTM D2983. Absolute viscosity is reported in centipoise (cP), equivalent to mPa Based on the internal resistance to rotation provided by the shear stress of the oil, the oil’s absolute viscosity can be determined. In this test method, the oil is placed in a glass tube, housed in an insulated block at a fixed temperature (Figure 2).Ī metal spindle is then rotated in the oil at a fixed rpm, and the torque required to rotate the spindle is measured. Additionally, 100☌ reduces the rise of measurement interference for engine oil soot contamination.Ī less common method of determining an oil’s viscosity utilizes a rotary viscometer. Likewise, most engine oils are typically measured at 100☌ because the SAE engine oil classification system (SAE J300) is referenced to the kinematic viscosity at 100☌ (Table 1).
#KINEMATIC TIMES DYNAMIC VISCOSITY MEANING ISO#
For most industrial oils, it is common to measure kinematic viscosity at 40☌ because this is the basis for the ISO viscosity grading system (ISO 3448). Typically, the viscosity is reported at one of two temperatures, either 40☌ (100☏) or 100☌ (212☏). Stating an oil’s viscosity is meaningless unless the temperature at which the viscosity was measured is defined.
#KINEMATIC TIMES DYNAMIC VISCOSITY MEANING MANUAL#
When used correctly, these viscometers are capable of reproducing a similar level of accuracy produced by the capillary tube manual viscometer method. In most commercial oil analysis labs, the capillary tube viscometer method described in ASTM D445 (ISO 3104) is modified and automated using a number of commercially available automatic viscometers. The viscosity is typically reported in centistokes (cSt), equivalent to mm2/s in SI units, and is calculated from the time it takes oil to flow from the starting point to the stopping point using a calibration constant supplied for each tube. This procedure is described in ASTM D445 and ISO 3104.īecause the flow-rate is governed by resistance of the oil flowing under gravity through the capillary tube, this test actually measures an oil’s kinematic viscosity. The narrow capillary section of the tube controls the oil’s flow rate more viscous grades of oil take longer to flow than thinner grades of oil. The suction is then released, allowing the sample to flow back through the tube under gravity. In this method, the oil sample is placed into a glass capillary U-tube and the sample is drawn through the tube using suction until it reaches the start position indicated on the tube’s side. The most common method of determining kinematic viscosity in the lab utilizes the capillary tube viscometer (Figure 1). However, for other oils, such as those containing polymeric viscosity index (VI) improvers, or heavily contaminated or degraded fluids, this relationship does not hold true, and can lead to errors if we are not aware of the differences between absolute and kinematic viscosity.įor a more detailed discussion on absolute versus kinematic viscosity, refer to the article “ Understanding Absolute and Kinematic Viscosity” by Drew Troyer. However, it is the oil’s resistance to flow and shear due to internal friction that is being measured in this example, so it is more correct to say that the gear oil has a higher absolute viscosity than the turbine oil because more force is required to stir the gear oil.įor Newtonian fluids, absolute and kinematic viscosity are related by the oil’s specific gravity. The force required to stir the gear oil will be greater than the force required to stir the turbine oil.īased on this observation, it might be tempting to say that the gear oil requires more force to stir because it has a higher viscosity than the turbine oil. Use the rod to stir the oil, and then measure the force required to stir each oil at the same rate.
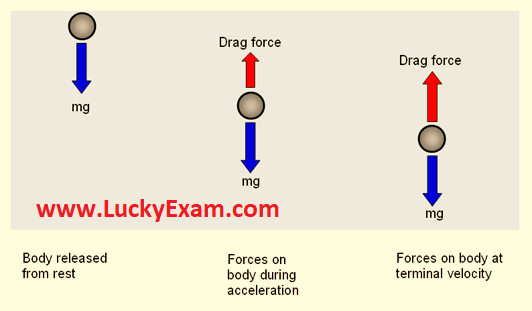
To measure absolute viscosity, insert a metal rod into the same two beakers. Which one will flow faster from the beaker if it is tipped on its side? The turbine oil will flow faster because the relative flow rates are governed by the oil’s kinematic viscosity. Imagine filling a beaker with turbine oil and another with a thick gear oil. An oil’s kinematic viscosity is defined as its resistance to flow and shear due to gravity.
